Premier Aluminum Llc - An Overview
Table of ContentsThe Main Principles Of Premier Aluminum Llc Premier Aluminum Llc - TruthsThe Single Strategy To Use For Premier Aluminum LlcIndicators on Premier Aluminum Llc You Need To Know
(https://comicvine.gamespot.com/profile/premieraluminum/)Utilizing low expense and unqualified providers can create quality problems, and wasted time and cash in the lengthy run. To assist you with the process, right here are some points to take into consideration when selecting the ideal metal spreading vendor.
A company that only uses the investment casting procedure will certainly attempt to market you on why that process is best for your application (Foundry near me). What if making use of the sand casting procedure is best for you and your demands? Instead, look for a supplier that provides a variety of casting processes so the very best option for YOU is chosen
If working with a solitary source for every one of your casting requires is important to you, the supplier needs to be varied in its capabilities. When incorporated with other integrated capacities, this can aid streamline and press the supply base. When selecting the right spreading vendor, cautious factor to consider needs to be provided to high quality, service, and price.
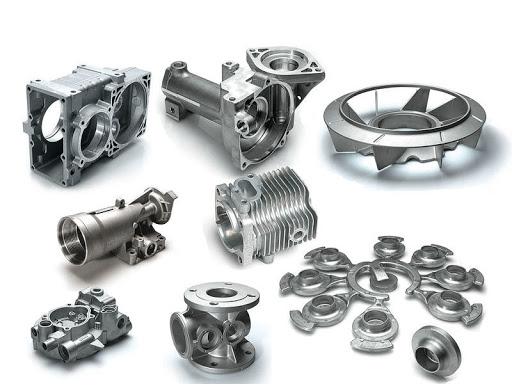
Premier Aluminum Llc for Dummies
Customers increasingly pick spreading providers who have machining capabilities. If the casting distributor discovers a problem throughout machining, the trouble is fixed much faster with no conflict over whose fault it is.
What do you need from your spreading provider? Are you looking for somebody to just provide a steel component to your front door or do you need much more?
Others will exceed the letter of the PO to help you conserve money and time. Do you have demands for both ferrous and non-ferrous alloys? Some factories are limited or specialized. Make sure the distributor can satisfy all your material or alloy requirements to get rid of the demand for several providers.
The Ultimate Guide To Premier Aluminum Llc

Study the supplier's website. Speak to a sales representative or business partner. Ask a great deal of concerns. See their facility. Obtain an understanding of what they can do for you and if you can see yourself building a solid, common relationship with them.
Light weight aluminum is also lightweight and has great deterioration resistance, making it excellent for applications where weight and resilience are crucial factors. In addition, light weight aluminum spreading is a cost-effective technique of manufacturing, as it calls for less power and resources than other techniques. Iron casting, on the various other hand, involves putting molten iron right into a mold to develop a preferred shape.
The Best Guide To Premier Aluminum Llc
Iron spreading is likewise able to stand up to heats, making it appropriate for usage in applications such as engine components and industrial machinery. Iron casting can be a lot more pricey than light weight aluminum casting due to the higher cost of raw products and the power required to melt the iron. When choosing between light weight aluminum casting and iron casting, it is important to take into consideration the certain demands of the application.
If stamina and resilience are more crucial, iron spreading may be the far better alternative. Other factors to consider include cost, manufacturing quantity, and lead time. To conclude, both aluminum casting and iron casting have their very own unique benefits and drawbacks. By very carefully considering the details demands of the application, makers can select the very best process for their product.ZheJiang Dongrun Casting Industry Carbon Monoxide,. Ltd was constructed in 1995, We have been in the spreading industry for even more than 25 years. Die casting is the name provided to the
procedure of developing complicated metal components via use molds of the element, also understood as passes away. The procedure uses non-ferrous steels which do not consist of iron, such as light weight aluminum, zinc and magnesium, because of the desirable residential or commercial properties of the steels such as low weight, higher conductivity, non-magnetic conductivity and resistance to deterioration. Pass away spreading production is quickly, making high production levels of parts simple.
It produces even more components than any kind of other process, with a high level of accuracy and repeatability. For more information about die casting and pass away casting materials made use of while doing so, read on. There are three sub-processes that drop under the classification of die spreading: gravity die casting (or permanent mold and mildew casting), low-pressure die spreading and high-pressure die spreading. The pure steel, additionally understood as ingot, is added to the heating system and maintained the molten temperature level of the steel, which is then movedto the injection chamber and injected into the die. The stress is then maintained as the metal solidifies. When the steel solidifies, the cooling procedure starts. The thicker the wall of the component, the longer the cooling time as a result of the quantity of indoor metalthat additionally needs to cool. After the part is fully cooled, the die cuts in half open and an ejection system presses the element out. Adhering to the ejection, the die is shut for the following injection cycle. The flash is the additional material that is cast throughout the process. This must be trimmed off utilizing a trim device to
leave just the primary part. Deburring eliminates the smaller sized pieces, called burrs, after the cutting process. Finally, the element is polished, or burnished, to provide it a smooth finish. This confirmed to be an inaccurate test, since the tester might cut into a piece and miss an area with porosity. Today, top producers utilize x-ray screening to see the entire inside of components without cutting right into them. This allows them to more precisely approve or turn down elements. To reach the finished item, there are 3 main alloys utilized as die casting material to choose from: zinc, aluminum and magnesium. Zinc is just one of one of the most pre-owned alloys for die casting as a result of its reduced cost of raw products.